|
|
|
|
|
|
|
 |
|
|
|
 |
|
본 장은 미국(美國)의 AT&T사(社)에서 마련된 체계적인 정전기 대책과 그 시행에 있어서 중요한
변수(Key factor)에 대한 소개입니다. 4장에서 소개한 Lockheed사(社)의 사례에 더하여,
AT&T사(社)의 계획수행 과정은 국내업체의 품질,안전담당자들에게 큰 도움이 되리라고 확신합니다.
● 서 론
AT&T사의 정전기 대책은 근 6년간 많은 시행착오를 거치면서 확립되었습니다. 처음에는 작업조건에
대한 정밀한 실험을 실시한 후, 연속된 모의실험(Pilot experiment)을 실시, 이상의 결과를
토대로 전 작업장 레벨로 확산시켰습니다. 그 과정에서 얻은 가장 중요한 교훈은 계획 못지 않게 그 시행의
묘를 살려야 한다는 점이었습니다. 따라서 본 장에서는 계획의 입안 및 그 수행이라는 두 가지 측면을 강조하여
소개하고자 합니다.
1991년에 회사에서 실시한 불량 원인조사(Failure analysis)에 의하여 Hybrid 직접회로(HIC)의
필름저항의 파괴가 정전기 피해에 기인하는 것이 발견되었습니다. 이후 수행된 여러 제어된 조건하의 실험을
통하여 ESD에 대한 방지책이 있는 경우의 불량율이 없는 경우보다 2~5배 줄어든다는 것을 알게 되었습니다.
통계적인 T-test 방법은 90~99.9%의 상관도를 보여주었습니다. 또한 실험 Data에서 정전대책이
최근 개발된 부품은 물론, 덜 민감한 부품에 대해서도 원가 감소에 좋은 영향을 미치는 것이 밝혀진 바,
한 공식보고에 의하면 투자비용의 950%가 회수되었습니다.
이상의 결과를 공식적으로 인정받기 위하여 외부로 납품되는 회로기판(Circuit Pack)의 성능이 체크되었는데
우선 Q.A.부에서 CP를 샘플링 하여 24시간 작동시킨 후 불량을 검출하였습니다. 검출된 불량품의 원인을
분석하여 그 원인 및 대비책을 보고서로 작성하고, 원인이 HIC에 의한 경우를 다시 모아 시간적으로 통계처리하여
그림 5-1.을 얻었습니다.
|
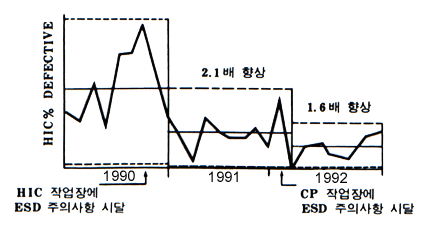
그림 (1) 납품되는 CP의 표본검출 조사결과 (전체 4배의 향상)
|
그림은 전체 HIC의 수에 대한 불량율을 퍼센트(%)로
나타낸 것입니다. 여기서 1990년도 후반의 급격한 감소는 적절한 정전대책의 실시 시기와 정확한 일치를 보여주고
있음을 주의해야 합니다. 1992년의 불량율은 원 년도에 비하여 5배정도 줄었으며 이는 그 전에 얻은 모의실험의
결과와 일치하고 있습니다.
이상의 결과를 토대로 전 공장에 ESD방지시설의 설치가 절실하였는데 이런 규모의 투자를 위해서는 경영
지도층의 지지가 필수적이었습니다. 1992년에 지도층에게 보고된 후 이후 계속 지도층의 폭넓은 지지로 ESD
대책의 시행이 계속되고 있습니다. 이것은 정전기 대책의 성공을 위해서는, 지도층의 열렬한 지원이 필수적이며
그것 없이는 그 운용에 있어 결국은 실패할 것이기 때문입니다.
ESD대책의 수행으로 AT&T사는 품질향상과 더불어 원가절감은 물론 더욱 중요한 것을 얻게 되었습니다.
그것은 고객들이 AT&T사 직원들이 제품을 다루는 정성과 조심성을 보고 신뢰 감이 커졌다는 사실입니다.
고객들이 내사(內社)했을 때 공장을 시찰하도록 주선한 결과 Wrist Strap을 차고 Anti-Static
Cushioning을 조심스럽게 다루며 작업하는 작업자들이야말로 그들에게는 품질의 가장 좋은 표현이기 때문입니다.
|
 |
|
AT&T社의 정전기 대책의 수립은 기본적으로 Bell연구소의 연구자료를 기본으로 하였고, 현실성과
작업자의 호응 예상도를 고려하여 이루어졌습니다. 이 외에도 기술의 발전에 따를 융통성도 중요하게 다루어졌습니다.
정전기 피해의 원인 규명을 위한 모델링은 크게 세가지를 이용했는데 아래와 같습니다.
① C D M ( Charge Device Model )
② H B M ( Human Body Model )
③ F I M ( Field Induced Model )
이상의 모델로부터 피해 메카니즘을 규명하여 적절한 대비책을 세워야 합니다. 왜냐하면 적절하지 못한 장비의
선택은 오히려 새로운 피해를 유발할 수 있기 때문입니다. 예로써,작업대 표면의 경우 ②,③항의 모델은 작업표면을
도체로 하는 것을 요구하지만, ①의 피해는 이 경우 최대가 되는 것입니다. 즉, CDM은 대전된 Device의
도체표면이 다른 도체표면을 접촉할 때 발생하는데 도체는 이런 경우 제일 좋지 않은 물질이기 때문입니다.
보통의 파괴 메카니즘은 ①항이 제일 많습니다.
결국, 각 작업장에서 피해 메카니즘 및 경제적인 효율을 고려하여 무슨 방지장비를 사용 하느냐를 결정해야
합니다. 방지장비의 물질은 크게 세가지로 분류됩니다
ⓐ Conductive (전 도 성) ( ρs ≤ 105 [Ω/sq] )
ⓑ Static Dissipative (정전 분산) ( 106 ≤ ρs ≤ 109 [Ω/sq] )
ⓒ Antistatic (제 정전기) ( 1010 ≤ ρs ≤ 1013 [Ω/sq] )
보통의 경우, ⓑ항의 물질이 무난하며 Table-mat도 ⓑ항의 물질이 제일 적합합니다. 그러나, ⓐ~ⓒ항의
물질은 각각 사용할 분야가 있으며 그의 선별이 중요한 것입니다. 일반적으로 사용되는 각 분야별 방지 물질은
한국 엠엠피 발행 『 정전기 제어 시스템 』(제1권- 3장- ESD 방지재료) 을 참고
하십시오.
|
 |
|
ESD 방지기술은 생산라인의 모든 부품에 지속적으로 수행되어야 하는데 이는 두 가지로 설명될 수 있습니다.
첫째, 작업자는 향상된 품질로 인하여 인식을 새롭게 할 수 있겠고
둘째, 고용주는 생산품의 품질을 쉽게 알 수 있어 관리가 용이해지기 때문입니다.
방지기술의 중요한 기본은 아래와 같습니다.
첫째, 모든 Item을 ESD에 민감하다고 가정해야 합니다.
둘째, 적절한 Grounding 없이 Item을 접촉하지 말아야 합니다.
셋째, 정전기 안전구역에서는 함부로 운반하거나 보관,취급을 삼가합니다.
이상의 원칙을 기본으로 AT&T 의 방식을 그림 2. 에 보였습니다.
|
ITEM
|
DEVICE CLASSIFICATION
|
IA
|
I
|
II
|
III
|
DEVICE SENSITIVITY
|
0~500V
|
0~1,999V
|
2,000~3,999V
|
4,000V +
|
Personnel awareness
|
R
|
R
|
R
|
|
Auditing compliance to ESD
|
R
|
R
|
R
|
|
Personnel grounding
|
R
|
R
|
R
|
|
Transporting product
|
R
|
R
|
R
|
|
Static-safe package
|
R
|
R
|
R
|
|
Static-safe bags
|
R
|
R
|
X
|
|
Static-safe tubes
|
R
|
R
|
X
|
|
Static-safe tote boxes
|
R
|
X
|
X
|
|
Dissipative mats,table tops
|
R
|
R
|
X
|
|
Conductive floors
|
R
|
R
|
X
|
|
Other controls(as required)
|
|
Air ionizers
|
R
|
X
|
X
|
|
Dissipative goldfinger shunts
|
R
|
X
|
X
|
|
Conductive cart
|
R
|
X
|
X
|
|
Antistatic smocks
|
R
|
X
|
X
|
|
Conductive packing
|
R
|
X
|
X
|
|
Conductive foam
|
R
|
X
|
X
|
|
표(1) ITEM 의 등급에 따른 ESD 방지대책
(NOTE: R=반드시 필요 X=엔지니어의 선택에 따라 가능함)
|
그림 (2) 에서 보듯이, 각 작업장에서 다루어 지는 Item의 등급에 의하여 적절하게 방지 장비를 선택해야
합니다. 모든 등급에 공히 필요한 사항은 작업 인력에 대한 훈련, 회계분석, 인력의 Grounding,
정전기 방지 운반기계, 정전기 방지 포장재 등입니다.
작업자의 Grounding은 Wrist Strap 이나 Heel Strap을 이용하고 1 MΩ의 저항으로
안전사고를 방지하였습니다. 특히 Wrist Strap은 작업자의 호응에 따라 그 성패가 결정되는 바, 미리
교육에 의하여 그 필요성을 강조하였고 이를 내규로 정하였습니다. 경우에 따라 도전성 바닥재와 이온성 공기
조화기로 작업자의 불편과 실수로 인한 피해를 방지했습니다.
Class IA, Ⅰ의 경우 Dissipative 물질이 필요하며 A 의 경우 특히 Static-safe
tote box가 필요함에 유의하십시오. 그러나 새로운 Tote-box 구입시 Static-safe type이
유리하며 새로 시판되는 Tote-box는 Circuit Pack을 운반상자의 Slot에 끼워 Coupling
coefficient를 줄이게 되어 있습니다.
그림 (2) 외에 방지시설은 엔지니어의 판별로서 선택될 수 있을 것입니다.
|
 |
|
ESD에 의한 피해가 공장의 제품불량에 주 원인으로 확인되면 이상에서 설명한 ESD대책이 잘 수행되도록
디자인에서 소비자의 레벨까지 철저한 수행이 수반되어야 합니다.
● 정전기
대책위원회 (ESD Committee)
ESD Plan의 수행에 있어서 종업원 및 지도층의 팀웍이 중요하고, 책임소재가 분명해야 하며, 수행 주체가
반드시 필요하므로 이를 24시간 담당하는 조정자(Coordinator)가 반드시 필요하게 됩니다. 이런
이유로 엔지니어링, 품질담당, 제어담당, 안전, 재료, 훈련담당자들이 보여 대책위를 구성하였는데, 이상의
임무와 더불어 각 부서간의 고유영역에 따른 정보 및 아이디어가 부서간의 갭에 구애되지 않고 전달되는 효과를
거두었습니다. 또한, 대책위의 규모가 너무 큰 관계로 산하에 소추진위를 구성하여 자주 모임을 갖고, 서로간의
견제를 도모하여 수행에 만전을 기했습니다.
|
● Implementation
of Facilities
장비, 시설의 선정 및 설치를 위하여 社內실험실을 두어 견본의 성능을 검토하여 납품업체를 선정한 후, 정전기
대책위와 실험실 그리고 납품업체간의 아이디어를 교류하여 매우 좋은 결과를 얻었습니다. 한 예로 폴리스틸렌을
이용하여 표면뿐만 아니라 내부도 Anti-Static 특성을 갖도록 하는 방법이 한 포장 연구담담에 의하여
제시되었는데 이로서 효과적인 정전기 방지는 물론 큰 원가절감 효과도 거두었습니다.
이외에도 사내(社內) 표준을 만드는 것이 필수적이며 각 방지장비의 정기적인 성능 체크를 해야 하는데 Wrist-Strap은
매일, Table-Mat는 월 한번씩 실시하였습니다.
|
● 작업자의
훈련 (Awareness/Training)
ESD Program의 지속적인 성공을 위해서는 작업인력에 대한 훈련이 제일 중요합니다. 예로서, Wrist
Strap의 경우“ 도대체, 왜 ”라는 질문에 대한 해답 없이는 착용을 귀찮아 할 것이기 때문입니다.
AT&T 에서는 최초의 1시간 정도의 교육으로 재미있게 만든 기술정보 비디오를 사용하여 정전기의
위험을 주지시켰습니다. 특히, 기술적인 내용의 경우 예컨데 MOS 트랜지스터의 경우 복잡한 숫자 보다는
간단한 Curve Tracer를 이용하여 오 작동을 가시화(Visualize)하였습니다. 이후 차츰 심도있는
교육과 병행하여 사내(社內)게시판을 통하여 수행현황 및 새로운 개술정보, 그리고 각 부서에서 거둔 효과를
홍보하였으며, 또 작업인력의 부서별 심도있는 교육 중의 지적을 다시 반영하는 순환을 되풀이 하여 사원교육에
성공하였습니다.
|
● Enforcemant
이상에서 설명한 교육과 더불어 작업자의 계속된 주의환기 및 책임소재의 필요로 인하여 감사기구를 두어 이들로
하여금 수시로 현장을 감독, 수행실태를 대책위에 보고 하도록 하였습니다. 각 생산라인의 검사는 매일 실시되었으며
위반사례는 체크되어 그 원인 및 대책이 논의되어 개선 되도록 하였습니다. 특히 검사시에는 작업자를 격려하는
방향으로 보고서를 작성하는 것이 중요했는데 그 서식은 아래 그림 5-3. 과 같습니다.
|
그림 (2) 품질관리 보고서식
|
이상의 검사와 더불어 수시로 회계처리하여 검사 Data의 적합성 여부를 확인하였으며, 필요한 경우 작업인력에
대한 추가 훈련을 실시하였습니다.
|
|
|
|
|
|
|
|